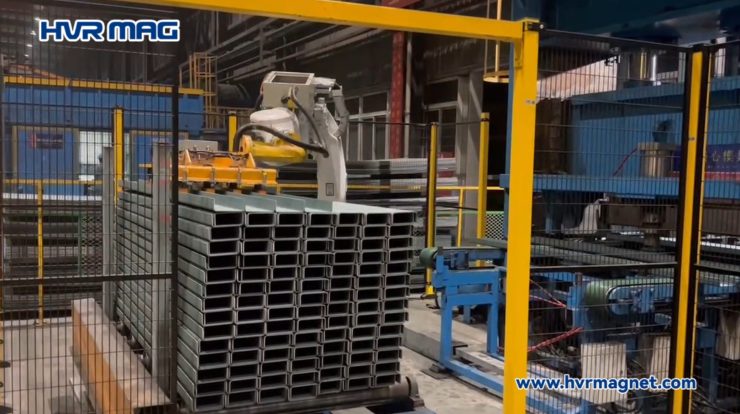
In the world of industrial automation, finding the right end effector for your application can make all the difference in efficiency, safety, and productivity. While electric magnetic end effectors have been a common choice in the past, they come with a set of disadvantages that can impede smooth operations and pose risks to the process.
Disadvantages of Electric Magnetic End Effector:
Workpiece Slippage: One common issue with electromagnetic end effectors is the risk of part slippage when moved quickly. This can lead to inaccuracies, delays in production, and potential damage to the workpiece.
Chip Retention: Machining chips have a tendency to stay on the gripper when unloading the piece with electromagnetic end effectors, causing cleanliness and debris management challenges.
Magnetization of Parts: Handled parts can retain magnetization when using electromagnetic end effectors, which can be undesirable in certain applications and may lead to further complications down the line.
Power Failure Risk: In the event of a sudden power failure, electromagnets lose their magnetism, resulting in the workpiece falling and potential safety hazards in the workplace.
How Electro Permanent Magnetic End Effector Solves These Problems: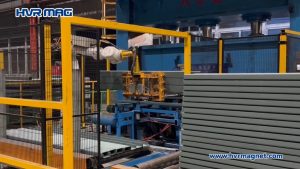
Strong and Uniform Holding Force: Electro permanent magnetic end effectors boast a powerful holding force of up to 16kg/cm2, with the magnetic force remaining constant over time without any decay.
Rapid Magnetization and Demagnetization: With magnetization and demagnetization times ranging from 0.6 to 3 seconds, electro permanent magnetic end effectors can efficiently grip and release workpieces with precision and speed.
Demagnetization Mechanism: During demagnetization, the electro permanent magnetic end effector generates an alternating magnetic field to demagnetize the workpiece effectively, eliminating any residual magnetism.
Safety in Power Failure Situations: By relying on permanent magnetic forces to hold the workpiece in place, electro permanent magnetic end effectors operate in a completely non-electrified state when gripping, mitigating the risk of workpiece displacement in cases of sudden power loss or cable damage.
Conclusion
Embracing the advanced capabilities of electro permanent magnetic end effectors can revolutionize your automation processes, offering unparalleled reliability, efficiency, and safety advantages over traditional electromagnetic solutions. Say goodbye to the limitations of electromagnetic grippers and welcome a new era of precision and performance with electro permanent magnetic end effectors. For more information, feel free to reach out to HVR MAG at export@hvrmagnet.com