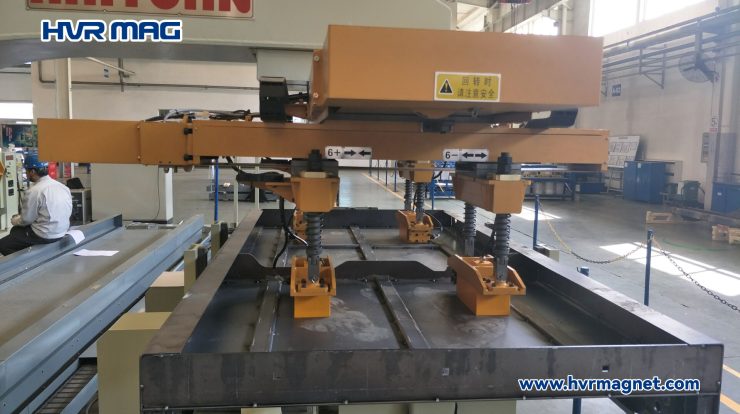
In recent years, the automation and smart technology sectors have witnessed significant advancements, particularly with the introduction of electro permanent magnetic grippers. These innovative devices have revolutionized the way industries handle materials, providing enhanced safety, efficiency, and versatility. Today, we will explore a specific case study involving the use of electro permanent magnetic grippers for transporting various profiles and rails in an automated workshop setting.
Case Study of Magnetic Grippers
Our client approached us with a unique challenge: they needed to transport aluminum profiles ranging from 4 to 6 meters in length, including 1.5mm thick patterned plates, as part of their production process. The requirements included not only horizontal transportation but also the capability to flip the materials 90 degrees for painting purposes. This necessitated a reliable and efficient gripping solution to ensure the safe handling of these components.
The Technical Challenge
Given the varying lengths and weights of the materials involved—rails weighing up to 140 kg and profiles around 40 kg—it was crucial to select the right electro permanent magnetic grippers to meet the operational demands. The primary challenge was to securely grip the thin patterned plates without causing deformation during the flipping process. Additionally, the long, narrow dimensions of the profiles required careful consideration of the gripping layout to ensure optimal magnetic force.
Magnetic Grippers Implementation
To address these challenges, our technical team conducted a thorough analysis of the client’s handling needs and selected appropriate electro permanent magnetic grippers:
- Thin Plate Handling: For the 1.5mm patterned plates, we opted for the P30B model, specifically designed for strong gripping of thin materials. By utilizing two sets of these grippers, we ensured that the gripping force would be sufficient to handle the plates safely, with a calculated safety factor of over 3.5 times the required gripping force.
- Long Profile Transportation: For the longer profiles, which varied in length from 4 to 6 meters and had a width of only 40mm, we arranged the electropermanent magnetic grippers in a linear configuration. This layout maximized the magnetic gripping surface area, employing three grippers to ensure a firm hold on the materials during transport.
- Safety and Reliability:Understanding the potential for slight deformation during the flipping process, we increased the number of magnets used to enhance the overall gripping strength. This precaution ensured that the materials would remain securely in place throughout the handling process, significantly reducing the risk of accidental drops.
Conclusion
As automation continues to evolve, the integration of advanced technologies like electro permanent magnetic grippers will play a vital role in streamlining operations, improving safety standards, and optimizing material handling processes across various sectors. As more companies recognize the benefits of these systems, we can expect to see a broader adoption of electro permanent magnets in the automation landscape.