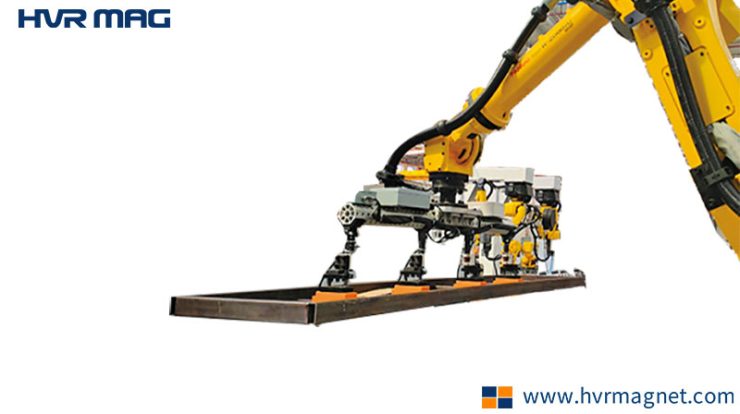
The magnetic gripper has revolutionized the way materials are handled in many industries. This innovative technology uses powerful magnets to pick up and move objects. Making it faster, more efficient, and safer than traditional material handling methods. The magnetic gripper is suitable for use in a wide range of applications.
Where the magnetic gripper has been particularly effective
Manufacturing: Magnetic grippers are commonly used in manufacturing to pick up and move sheet metal, pipes, and tubes. The grippers can be attached to robotic arms, allowing for precise and efficient movement of parts on the production line.
Warehousing and logistics: They are also used in warehousing and logistics to move heavy metal objects. The grippers can be attached to forklifts or cranes, allowing for safe and efficient movement of materials around the warehouse.
Recycling: Magnetic grippers are used in recycling facilities to separate ferrous metals from non-ferrous metals. The grippers can pick up and move metal objects, allowing them to be sorted and processed more efficiently.
Construction: Magnetic grippers are used in the construction industry to move large metal objects, such as steel beams and pipes. The grippers can be attached to cranes or other heavy machinery, allowing for safe and efficient movement of materials on the construction site.
Advantages that magnetic gripper offers
Increased efficiency: Magnetic grippers are much faster and more efficient than traditional material handling methods. They can pick up and move objects in a fraction of the time it would take a human worker to do the same task.
Improved safety: Magnetic grippers eliminate the need for workers to manually handle heavy or awkward objects. Reducing the risk of injury on the job. The grippers can also be used to move materials in hazardous environments. Such as nuclear power plants or chemical processing facilities.
Reduced maintenance: Magnetic grippers require very little maintenance. As they have no moving parts that can wear out or break down. This can result in lower maintenance costs and less downtime for repairs.
Versatility: Magnetic grippers can be used with a wide range of materials. Including ferrous metals, non-ferrous metals, and even some plastics. This makes them a versatile solution for many different material handling applications.
Example of using magentic gripper
The magnetic gripper of HVR MAG have many amazing examples of collaboration. For example, the magnetic gripper we designed for a construction machinery company. It is not very large, but can grip large size curved corrugated plates for top installation in bridge caverns, tunnels etc. During installation tests it showed good performance, gripping the workpiece quickly and stable, without sliding or wobbling even when the workpiece was turned 180°. It is also very simple in its own construction and does not affect the working stroke of the robot arm at all. Combined with the safety and energy-saving advantages of electro-permanent magnet technology, the customer is very satisfied with the results of the magnetic gripper.
In conclusion, the magnetic gripper is a game-changer in material handling, offering increased efficiency, improved safety, reduced maintenance, and versatility in a wide range of applications. As this technology continues to evolve, we can expect to see even more innovative uses for magnetic grippers in the future.
For customised industrial automation solutions with the magnetic gripper, please contact us.