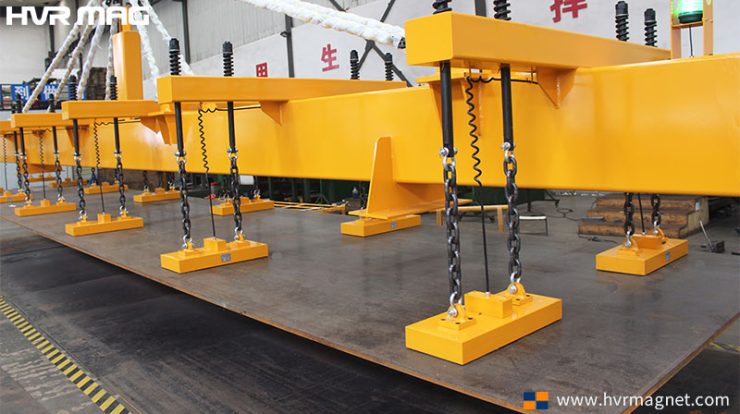
Sheet metal lifter is a specialised tool for handling sheet materials. The main categories are mechanical sheet metal lifter, vacuum lifter and magnetic sheet metal lifter. The handling of sheet metal materials may seem very simple, but in fact there are many small details to consider.
The main points to consider when handling sheet metal are
1.The thickness of the sheet metal
When metal plate is handled horizontally, it bends or deforms like paper under the influence of gravity. The thinner the plate, the greater the deformation. The deformation of metal sheets thicker than 10 mm will not be obvious. The consequences of deformation of thin sheets are much more severe than those of paper. If a sheet is badly stressed during handling, it can fall off very easily. The sharp edges and corners of the sheet can cause very serious damage. Therefore, when lifting thin metal plates, we must pay attention to the distribution of force points to ensure that the thin plate can be evenly stressed and to avoid interference from adhesion forces and inter-sheet deformation.
2. Length
The length of the plate is also important when lifting. If the sheet is less than 10mm thick, the unilateral overhang of the sheet must be less than 100mm, so if we want to lift a sheet 8mm thick and 10m long, the lifting length of the spreader should preferably be more than 8m. And it is safe to lift a sheet thicker than 10mm with a unilateral overhang of 150mm. Assuming that a medium thickness plate of 11mm thickness and 12m length is to be lifted, the lifting length of the spreader should be at least 9m.
3. Surface
The surface finish of sheet metals requires attention. Thin metal plates are usually smooth and require a high quality finish. We need to avoid leaving scratches on thin plates. Rougher surfaces can cause wear and tear on the vacuum sheet metal lifter.
How to choose the right sheet metal lifter?
Mechanical sheet metal lifter
This type of sheet metal lifter includes hooks and clamps and their upgraded versions. You can clamp the sides of the sheet and lift it. With this type of lifting, care must be taken to place pads or pallets on the underside of the sheet metal to avoid distortion, wear or dropping. This type of lifting requires the worker to manually adjust the position of the plate to ensure that the forces are evenly distributed. It is not as efficient or safe as the new technology. The main advantage is that there are few restrictions on the material and size of the sheet.
Vacuum lifter
Vacuum cups are very good at handling flat sheets of material. It does not wear the smooth surface of the sheet and does not restrict the material of the sheet. But it is more demanding on the surface. If your sheet metal is rough, or if there are metal chips on the surface, the vacuum cups will be very susceptible to abrasion. This reduces the safety of the handling process. You will need to replace the rubber ring frequently, increasing maintenance costs.
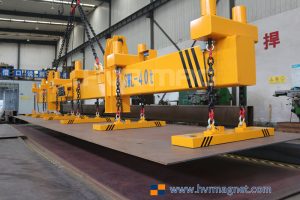
Magnetic sheet metal lifter
The magnetic sheet metal lifter is very safe and efficient. It grips the sheet and releases it very quickly, usually in a matter of seconds. The magnetic suction force is much greater than vacuum cups. The electric permanent magnets of HVR MAG have very strong suction force up to 16 kg per square centimetre. The magnetic sheet metal lifter is only used for handling magnetically conductive materials.
When buying a magnetic sheet metal lifter, you need to understand the difference between electromagnet, permanent magnet and electro-permanent magnet. Electromagnets use a lot of power and require a constant supply of power when handling materials. This in turn causes the magnets to heat up and reduce their magnetism. Therefore, if you are handling large quantities and working long hours, electromagnetic lifters should be considered with caution. Permanent magnets and electro-permanent magnets do not get hot over long periods and are safer than electromagnets. However, permanent magnets usually require manual plate release and are not very efficient. This makes electric permanent magnets a better choice.
Electric permanent magnets are 95% more energy efficient than electromagnets. The electricity is only used for the moment of pulling and releasing the plates. The EPM sheer metal lifter can be operated remotely, so even a plate weighing tens of tonnes can be easily lifted by one worker. The magnetic force level of the HVR MAG can be adjusted and the magnetic modules can be controlled in groups, so if you need to handle different sizes of steel plate, one magnetic lifter may be perfectly compatible.
As a specialist manufacturer of electro-permanent magnetic sheet metal lifter, HVR MAG offers a wide range of sheet metal lifter models. Telescopic beam and battery powered versions are also available. Please contact us for more information.