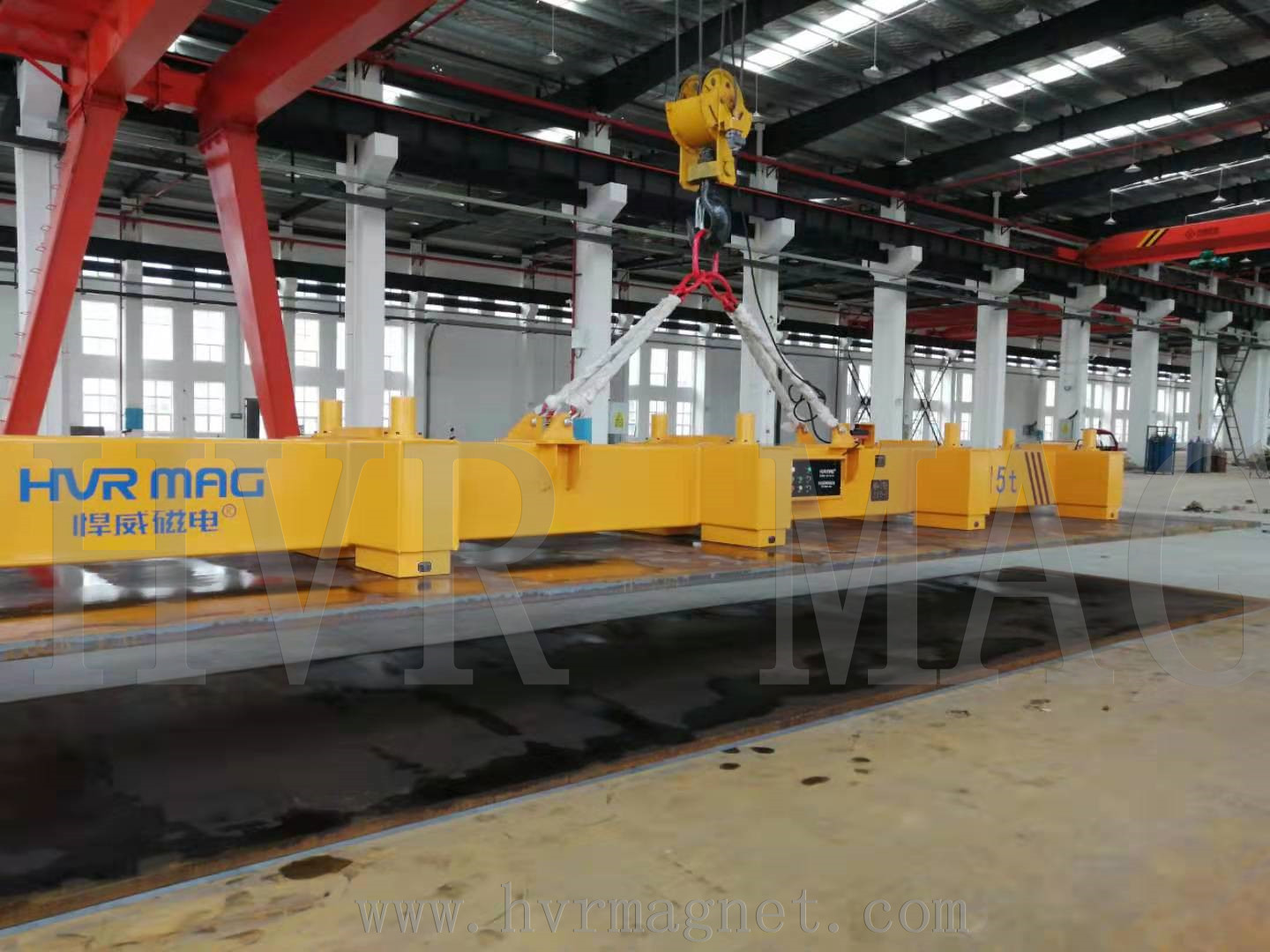
During the daily use of lift magnets, there are some inspection procedures for operators to bear in mind for lifting magnet repair, which can steer you from some avoidable problems and make them highly resistant to impact.
Nobody dares to claim that lifting magnets could never be damaged in any collisions. As a matter of fact, some parts of them could be worn off after years of use and would require to be replaced with new ones.
To repair or replace the parts inside or outside of a magnet lifter is not easy. Therefore, understanding certain inspection procedures of your lifting magnets to ensure they remain in compliance, becomes critical:
- Lift magnet surface
- Condition and operation of handles and safety latches
- Condition of lifting ball or eye hook
- Cracked housing, welds or loose bolts
- Warning labels and capacity markings
- Inspection of all other parts
- Replacement of any missing parts
- Repair/replacement of all damaged parts
- Replacement of warning labels and capacity markings
- Load testing
For scrap lifting magnet:
When completing a scrap or lifting magnet repair project, technicians should inspect/repair the following:
- Structural areas of the scrap magnet attachment
- The magnet’s copper or aluminum conductor
- Magnetic coils
- Insulation materials
- Sheaves or pulley wheels
- Hydraulic systems
For electro permanent lifting magnet repair:
- Inspection of lift magnet surface and control unit, and the remote
- Inspection of all other parts
- Repair/replacement of all damaged parts
It needs to the pointed out that the technicians must be experienced and skilled with the behaviour of magnetic field and its magnetic force installed in the main body of magnetic lifters. After completing the repair process, a full set of testing procedures should be conducted to ensure that the lifting magnet is operating properly.