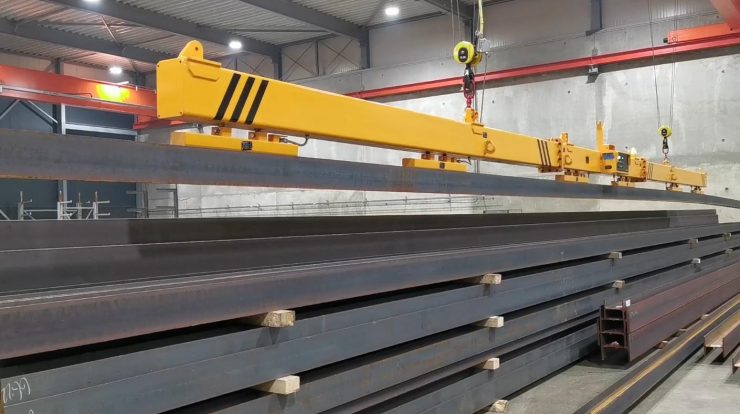
Now the permanent magnetic crane on the market are in a wide range of styles, and manufacturers are everywhere, but the product quality also varies; many users in the choice of permanent magnetic cranes can not judge the quality. Now according to our experience, we will tell most users how to identify the permanent magnetic crane.
We believe that the following aspects need to be considered.
- safety factor:
the safety factor of the permanent magnetic crane on the market now is roughly 2.5, 3.0, 3.5 several. The defined safety factor means the crane’s maximum pull-off force is several times the rated lifting capacity. For example, in Model: HM1 001, the rated lifting capacity is 100KG; if the safety factor is 2.5 times, then its maximum pull-off force is 250KG; if the safety factor is 3.5 times, then the leading pull-off force is 350KG. The more significant the safety factor, of course, the use more secure. That is the primary concern for the selection of a permanent magnetic crane. HVR produces permanent magnetic cranes, and the safety factor is more than 3.5 times; some even reach 4.0 times.
- Safety locking device:
The safety locking device is a safety device used to protect the magnetic circuit from being easily disconnected when the permanent magnetic crane is absorbed with the absorbed object and forms a magnetic circuit. Its structure is reasonable for the safe use of a permanent magnet crane is also visible. If the design of this device is not appropriate, in case it loses its role in the lifting process, causing safety accidents.
- internal magnetic structure
All manufacturers of permanent magnetic crane principles are the same, but there are differences in the magnetic circuit design. If the magnetic circuit structure is unreasonable, one is that the lifter may not guarantee the pull-off force, and the second is that the role of permanent magnets is not given full play, which may cause waste and thus increase costs.
- Flexibility of spindle rotation:
the flexibility of spindle rotation is directly related to the comfort of operation. If the spindle rotation is not flexible, that will be very hard to rotate the handle over time; the operator may be a brutal operation, resulting in permanent magnetic crane service life is not long, bringing the unnecessary waste to the enterprise. HVR has also made many improvements in this area to ensure the flexibility of the spindle rotation. Moreover, the magnets on the shaft are fixed by a brand new process to ensure that the magnets do not slide and have no abnormal noise when rotating.
- protection of the spindle hole:
permanent magnetic cranes are generally used in mechanical processing places around iron chips and dust, so now, in most permanent magnetic cranes in the use of a period, the spindle can not turn or even jammed. The reason is that the spindle hole inhaled many iron chips and dust, and the spindle stopped. HVR has made notable improvements in this area, using a novel dustproof structure to ensure that iron chips and dust do not enter the spindle hole to ensure the cleanliness of the spindle and spindle hole.
- Treatment of the contact surface:
The contact surface of the permanent magnetic crane must be finely ground so that the permanent magnetic crane can lift to the maximum extent with the object to be sucked when lifting, reducing the air gap and ensuring the maximum lifting capacity.
- rings:
most permanent magnetic cranes use welded rings; the safety factor meets the lifting equipment requirements. However, welded products will inevitably encounter problems after prolonged use, which may be a safety hazard. HVR has considered this by choosing high-quality alloy steel, using integral wire-cut or fine cast rings to minimize safety hazards on the rings and nickel-plated surfaces.
- the use of permanent magnets:
the use of permanent magnets in terms of the primary consideration of two aspects: one is the performance, performance can not meet the requirements, suction will not be guaranteed, the second is the surface corrosion, rare earth permanent magnets a significant weakness is poor corrosion resistance, so must do a good job of surface treatment. Some companies, to reduce costs, use permanent magnets without surface treatment, over time, the magnet surface oxidation rust, so that one is the endless magnetic crane lifting capacity will decline; the second is the spindle within the magnet oxidation falls off, it may cause the spindle jammed.
- the appearance of the permanent magnetic crane:
HVR crane shape and appearance are designed using industrial aesthetics;. However, the arrival of a permanent magnetic crane is not affected but can reflect a company’s attention to product quality. Ltd. in the production process of permanent magnetic crane, strict production according to the map, to ensure the size, tolerance, while each function on the parts has requirements, so the product is assembled, even if the surface is not painted, is a beautiful product. Of course, all permanent magnetic cranes from HVR are painted (including spraying and overall nickel plating) according to customer requirements before leaving the factory. The paintwork should also consider the appearance and should not show flow hanging, color difference, air holes, and crashing.
HVR are going to offer you high quality permanent magnetic cranes. If you are interested in it, please feel free to contact us.