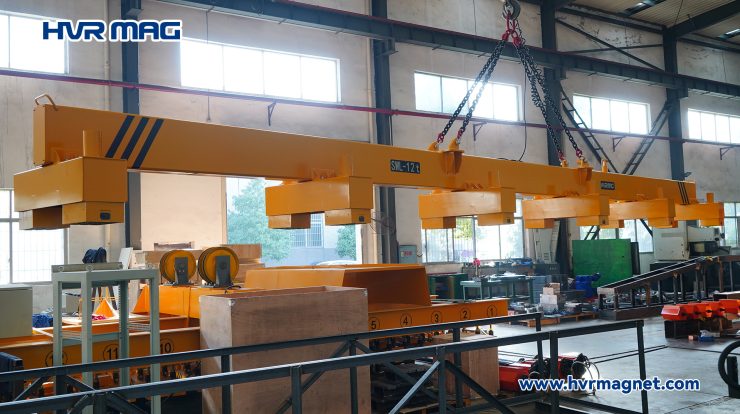
In the world of industrial manufacturing, efficiency, safety, and precision are paramount. A recent project we undertook highlights the transformative impact that electro permanent lifting magnets can have on operations, particularly in the steel plate processing industry. We designed a specialized lifting device tailored for steel plate shot blasting lines, showcasing the advantages of modern magnet technology.
Lifting Magnets Project Overview
For our client, we created a custom electro permanent lifting magnet specifically for handling steel plates on a shot blasting line. This lifting device was meticulously engineered to meet the specific needs of the steel plate processing industry. The device is capable of handling steel plates with dimensions ranging from 12,000 to 22,500 mm in length, 1,250 to 2,000 mm in width, and 6 to 10 mm in thickness, with a maximum lifting capacity of up to 4 tons.
The lifting device operates in a standard indoor environment with a bridge crane that has a single hook and a 10-ton capacity, featuring a lifting height of 10 meters. It supports two control methods: wireless remote control and manual operation, enhancing both flexibility and convenience.
Previous Handling Methods
Before implementing our electro permanent lifting magnet, the client relied on traditional steel ropes and hooks for lifting steel plates. This method was fraught with several issues:
- Labor-Intensive: Steel ropes and hooks required significant manual intervention. Workers had to manually pry and clamp plates, which was both time-consuming and physically demanding.
- Surface Damage: Traditional lifting methods often led to surface scratches and deformations on the steel plates, negatively impacting product quality.
- Safety Risks: The complexity and manual nature of the process increased the risk of workplace injuries and accidents.
Advantages of Electro Permanent Lifting Magnets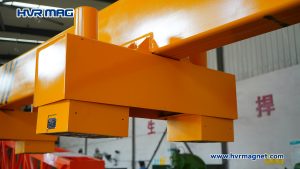
Our electro permanent lifting magnet provides numerous benefits over traditional methods:
- Speed and Convenience: The lifting magnet enables quick and efficient handling of individual steel plates without the need for extensive manual labor. It simplifies the process of positioning and lifting, significantly boosting productivity and reducing labor intensity.
- Versatility: The lifting magnet is designed to handle various steel plate sizes and thicknesses. Its powerful magnetic grip and adaptable control system ensure that each plate is lifted safely and precisely, regardless of its dimensions.
- Surface Protection: Unlike steel ropes and hooks, which can damage plate surfaces, the electro permanent lifting magnet adheres to the steel plates through a strong magnetic field. This method prevents surface injuries and deformations, preserving the quality of the steel plates and reducing subsequent processing issues.
- Cost-Efficiency and Safety: By reducing the need for manual handling, the electro permanent lifting magnet lowers labor costs and minimizes physical strain on workers. Additionally, the remote control feature enhances safety by allowing operators to remain at a safe distance from the lifting area, significantly decreasing the likelihood of accidents.
Conclusion
The integration of electro permanent lifting magnets into steel plate handling processes marks a significant advancement in industrial operations. By addressing the inefficiencies and safety concerns associated with traditional lifting methods, these magnets offer a more effective, versatile, and safer solution. As demonstrated in our recent project, the benefits are clear: enhanced productivity, improved product quality, and a safer working environment. As industries continue to evolve, adopting innovative technologies like electro permanent lifting magnets will be crucial in driving efficiency and safety standards to new heights.