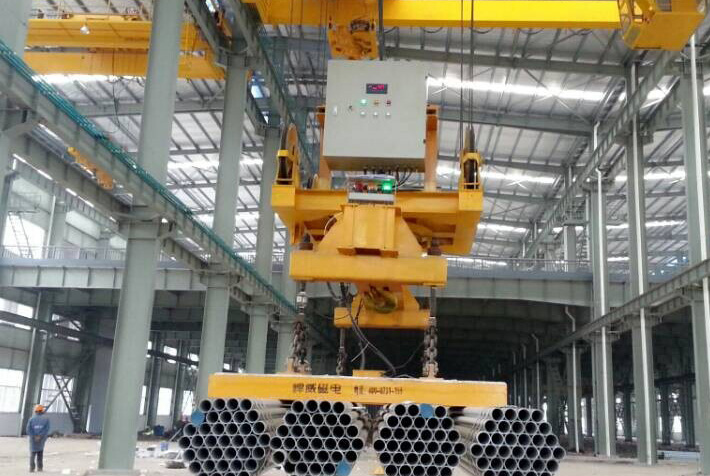
How to choose the right lifting magnet system for lifting steel plates, sheets, coils, slabs, tubes, pipes, steel scraps, steel bundles, etc.? HVR MAG explains the factors to consider and tips to take when making decision.
Lifting magnets may be electric, permanent or electro-permanent, and may be installed and used as single magnetic lifter or as arrangements of magnetic lifting systems. They are vital to steel industries including scrap yards and metal recycling, steel mill, steel fabrication, and manufacturing. Therefore, making an optimum selection of the right steel plate handling equipment can help improve manufacturing efficiency and productivity.
The load factors that dominate the lifting magnet system selection for any specific applications are:
▶Weight, shape, and contact area of the objects to be lifted.
▶Surface conditions of load.
▶Stiffness of load.
▶Range of sizes and shapes to be lifted.
▶Frequency of occurrence of the different sizes and shapes.
▶Adjustment of lifting power for less than full magnet face utilization.
▶Temperature of load material.
▶Ambient temperature.
First, know what and how much you’re lifting
As with any lifting operation, you must know the material you’re lifting. The material alone determines factors such as the number of magnets you’ll need and the magnet’s size. In most scenarios, a single magnet will do the job with ease, but there are times where an additional magnet would be wise. Such scenarios include lifting an extremely heavy material, or if you’re concerned you’re maxing out the magnet’s lifting capability.
Secondly, you must know how much you’re lifting – that is, the weight of the material
Identify your safe working load and stick to it. One of the many factors that goes into the weight of your material is its thickness. The item’s thickness will determine if your magnet can safely lift the material with a strong hold.
Third, decide which type of magnetic lifting technologies you’d like to employ
While you can’t go wrong with a permanent magnet, electromagnet, or electrically switched permanent magnet, there are some benefits to each. Most notably, an electromagnet requires a continuous power source, but you have the option to deactivate the magnet. On the other hand, a permanent magnet is always activated and doesn’t require a power source. As to the third type, EPMs do not require continuous power supply to work, neither do they consume any power during working – electric pulse is only needed for magnetization and demagnetization phase.
To conclude:
→For steel bundles like rebars, pipes, or other thick steel parts that requires deep penetration of magnetic fluxes to be picked up, electric lifting magnet system is preferred.
→For a safer & more energy-efficient way of heavy lifting, electro-permanent magnetic lifting system is recommended.
→For mobile & light lifting, permanent magnetic lifter is not a bad choice.
Picking the right lifting magnet system for your lift can make a difference between a successful lift and an accident. Consideration of each of these factors will lead to identification of the magnet type, shape, number, and system layout best suited for economy, efficiency, and safety.