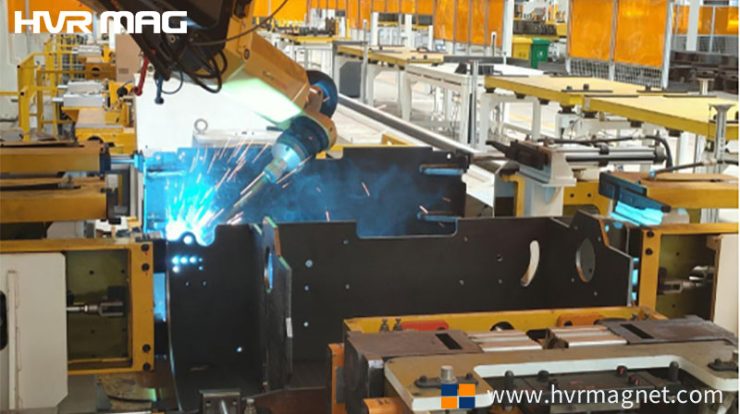
In the world of modern manufacturing, welding is a critical process that binds industries together. From automotive to shipbuilding, the quality and efficiency of welding can make or break a product. Enter electro permanent magnets, a groundbreaking innovation in welding fixtures that is transforming the way we approach welding assembly. With their unique combination of electromagnetic principles and permanent magnet properties, electro permanent magnetic grippers are setting new standards for precision, efficiency, and sustainability in welding.
What Are Electro Permanent Magnetic Grippers?
Electro permanent magnets are advanced fixtures that combine electromagnetic technology with the properties of permanent magnets. Unlike traditional mechanical fixtures, electro permanent magnetic grippers offer a simpler, more efficient way to hold workpieces in place during welding. By controlling the flow of electric current, operators can quickly and easily clamp or release workpieces, significantly reducing setup time and improving productivity.
Key Advantages of Electro Permanent Magnetic Grippers in Welding
- Simplified Operation
One of the standout features is their ease of use. With just the flip of a switch, operators can activate or deactivate the magnetic force, allowing for rapid clamping and releasing of workpieces. This eliminates the need for complex mechanical adjustments, saving valuable time and reducing labor costs.
- Strong and Stable Clamping Force
They deliver a powerful and consistent clamping force, ensuring that workpieces remain securely in place during welding. This stability is crucial for maintaining positional accuracy, which directly impacts the quality of the weld. By minimizing movement and vibration, these grippers help reduce welding defects and improve overall product quality.
- Adaptability to Complex Workpieces
Traditional fixtures often struggle with irregularly shaped or uneven surfaces, but electro permanent magnetic grippers excel in these scenarios. Their ability to conform to the shape of the workpiece ensures uniform clamping force across the entire surface. This adaptability is particularly beneficial in industries like automotive and shipbuilding, where workpieces can vary widely in size and shape.
- Energy Efficiency and Sustainability
These magnetic grippers are designed with sustainability in mind. They only consume electricity during the brief moments of magnetization and demagnetization. Once activated, they rely on the permanent magnet’s properties to maintain their grip, requiring minimal energy. This not only reduces operational costs but also aligns with the growing demand for eco-friendly manufacturing practices.
Applications Across Industries
Electro permanent magnetic grippers are making waves in a variety of industries, including:
Automotive Manufacturing: Used in body welding fixtures, electro permanent magnetic grippers improve precision and efficiency, ensuring consistent weld quality across vehicle frames.
Shipbuilding: In the assembly of ship hulls, they provide reliable clamping for large, complex structures, enhancing both safety and weld integrity.
Construction and Heavy Machinery: These grippers are ideal for welding large steel components, where stability and precision are paramount.
Challenges and Future Prospects
While these grippers offer numerous benefits, there are still some challenges to address. For instance, the initial cost of electro permanent magnetic grippers can be higher than traditional fixtures, which may limit their widespread adoption. Additionally, their performance can be affected in extreme environments, such as high temperatures or strong magnetic fields.
However, as technology continues to advance, these limitations are expected to diminish. Innovations in materials and manufacturing processes are likely to reduce costs and enhance the performance, making them accessible to a broader range of industries.
Conclusion
Electro Permanent Magnets are revolutionizing modern welding processes by offering a simpler, more efficient, and sustainable solution for workpiece clamping. Their ability to adapt to complex shapes, deliver consistent clamping force, and reduce energy consumption makes them an invaluable tool in industries ranging from automotive to shipbuilding.
As we look to the future, electro permanent magnetic grippers are poised to play an even greater role in driving the quality, efficiency, and sustainability of manufacturing processes. By embracing this innovative technology, industries can stay ahead of the curve and continue to deliver high-quality products in an increasingly competitive market.