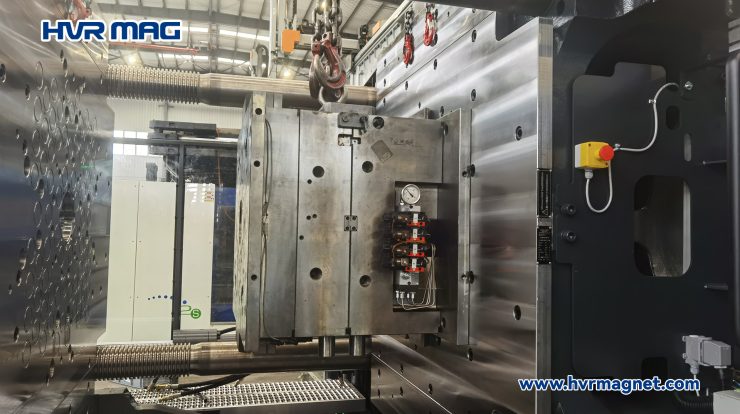
Injection molding is a widely used manufacturing process for producing plastic parts of all shapes and sizes. The heart of this process lies in the mold — a complex tool that requires careful maintenance to ensure efficient production and prolonged lifespan. Here are essential mold maintenance tips for the plastics injection molding industry:
Regular Cleaning: Proper cleaning after each production run prevents residue buildup, which can affect the mold’s performance and lead to defects in the molded parts. Use appropriate cleaning agents and tools to remove any plastic residue, rust, or other contaminants.
Inspection for Wear and Tear: Conduct regular inspections to identify wear and tear on the mold components such as ejector pins, guide pins, and bushings. Replace parts that show signs of damage to prevent more extensive issues that could halt production.
Lubrication: Lubricate moving parts and components to reduce friction and wear. Use high-quality lubricants recommended by the mold manufacturer and apply them according to the specified intervals.
Temperature Control: Maintain optimal temperature control during the molding process to prevent thermal stress on the mold. Sudden temperature fluctuations can cause deformation or cracking, leading to mold damage and poor product quality.
Storage and Handling: When not in use, store molds in a clean, dry environment to prevent rust and contamination. Use protective covers or coatings if necessary to maintain the mold’s condition. Handle molds with care to avoid any impact or mishandling that can result in damage.
Maintenance Records: Provide comprehensive training to personnel involved in mold maintenance to ensure they understand proper procedures and techniques. Continuous education on new maintenance practices and technologies is also beneficial for optimizing mold performance.
Increase Plastic Mold Maintenance Level with Magnetic Clamping System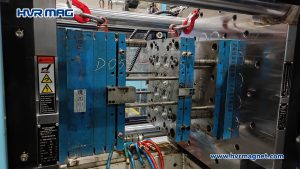
Mold clamping system also affects mold maintenance. Magnetic clamping systems offer several advantages over traditional mechanical or hydraulic clamping methods:
Quick and Easy Setup: Magnetic clamping systems eliminate the need for manual clamping mechanisms, significantly reducing setup time and streamlining mold changeovers.
Uniform Clamping Force: Magnetic clamps provide consistent and uniform clamping force across the entire mold surface, ensuring precise and reliable molding results.
No Wear or Leakage: With no moving parts or hydraulic components, magnetic clamping systems reduce the risks of wear and tear and leakage, keeping a safe and clean environment for injection molding.
Improved Mold Life: By reducing wear on mold components, magnetic systems can extend the lifespan of molds.
If you’re interested in upgrading your mold clamping system, consider exploring the benefits of a magnetic mold clamping system like HVR MAG.