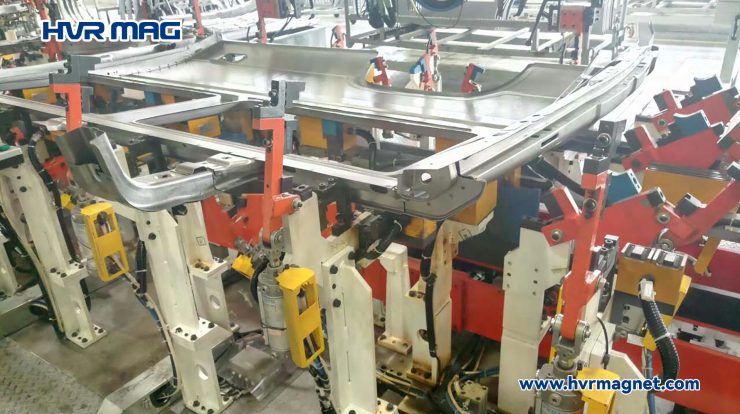
Electro permanent magnetic grippers are proving to be a key enabler in the automation of welding workstations. These magnets are used in conjunction with robotic systems, allowing for seamless integration and increased productivity. By ensuring precise workpiece positioning and reliable clamping, they reduce the need for manual intervention, effectively speeding up the welding process. The high degree of automation and flexibility offered by electro permanent magnets allows manufacturers to optimally utilize their resources and adapt to changing production requirements with ease.
Consideration of Electro Permanent Magnetic Grippers
- Maintain a distance of at least 5mm from the electromagnetic permanent magnet during welding to prevent the transmission of high temperatures that could lead to its malfunction.
- Control the electromagnetic permanent magnet in the welding station through a designated control system, understanding the working environment and how it coordinates with the system.
- Inform the magnetic gripper supplierabout the products used in the welding station to replicate them based on the product itself and prevent welding deformations.
Magnetic Residual Effects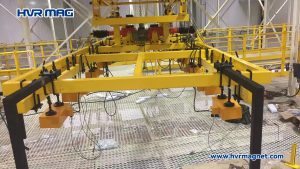
One of the prominent concerns in welding applications is the influence of magnetic residual effects. Electro permanent magnets undergo rigorous testing and are designed to meet strict industry standards. With proper design and placement, these magnets exhibit low levels of residual magnetism, ensuring minimal impact on the welding quality. Manufacturers can rely on the consistent magnetic field distribution and controlled magnetism of electro permanent magnets to achieve excellent weld results.
Comparing Electro Permanent Magnetic Grippers and Electromagnetic Grippers
The magnetic lines of electro permanent magnets are uniform, typically not exceeding 16mm when using a 50-magnet example, covering the product’s circumference. Unlike electromagnetic iron, electromagnetic permanent fixtures do not disperse magnetic forces, reducing the magnetization impact on the product.
Conclusion
When designing welding station fixtures, considering the application of electromagnetic permanent fixtures can offer stable clamping without the risk of sudden power interruptions due to wiring issues, ensuring product quality after welding. Moreover, their safety features address common pain points in welding applications, improving overall workplace safety. By optimizing clamping and mitigating magnetic residual effects, electro permanent magnets enable high-quality welds. As manufacturing facilities embrace the era of smart manufacturing, the adoption of electro permanent magnets in welding operations is set to redefine industry standards and drive further advancements.
For more information, please contact HVR MAG at export@hvrmagnet.com